Push-Back Racking (LIFO)
Push-Back Racking (AR Live Storage LIFO) is a live storage system for accumulation of pallets, just like the Live Pallet Racking FIFO system (AR Live Storage), but designed for LIFO type load management (last pallet in, first pallet out).
Push-back racking for pallets has a single loading and unloading area, at the front of the structure, and the unit loads are stored by pushing the previous ones towards the back of the rack.
Depending on the movement system used to move the pallets, there are two types of Push-Back Racking:
- Push-back with shuttles: In the system with shuttles, each pallet, except the last one, is deposited on a shuttle, which moves on rails with a slight incline.
- Push-back with rollers: The pallets are moved by means of roller beds fixed to the structure with a slight incline.
Like other live storage solutions, it is a high-density storage system, which optimises the available storage space. It can also be combined with other storage systems which makes it a versatile solution.
More information about Live Storage solutions on our Blog: Type of Live Storage systems




Push-Back Racking (LIFO)
The Push-back Racking system is a live storage solution for pallets formed by a compact structure, where unit loads are moved by means of rollers or shuttles with the aid of a slight incline.
It is a system especially designed for LIFO stock management (Last in, First out), where the last pallet placed on the rack is the first to be unloaded.
Unlike FIFO live storage, which needs one aisle for loading and another for unloading, in push-back racking, the forklift accesses the stored unit loads along a single work aisle.
Exerting a pushing force is used to place a new pallet, where the forklift pushes the unit loads already stored towards the back, making space for the new pallet to be deposited, hence the term “push-back”.
The unloading process uses the force of gravity, is performed in the same location as the loading and is similar to the FIFO type live storage. When the first unit load is unloaded, the following positions slide in a controlled way towards the unloading position.
Advantages and features of Push-Back Racking system (LIFO)
The main advantages of Push-Back Racking LIFO are its capacity to optimise the available space and its rapid loading and unloading of materials.
- Excellent use of space: As a live system it is a high-density storage solution, i.e. it optimises storage capacity for the same space.
- Ideal for homogeneous non-perishable products: When implementing the LIFO (Last in, First out) management system, the last unit load in is the first load out.
- Quick and easy loading and unloading: Since the forklift does not have to enter the aisle of the structure, manoeuvring and loading and unloading time is reduced.
- Safety: In addition to complying with all European quality standards, the LIFO push-back racking structure has a safety system for controlling and braking loads which minimises the risks in both the shuttle and roller system.
- Stock control: By allowing you to differentiate a different product reference in each loading aisle.
- Versatility and compatibility with other adjustable pallet racking systems.
- Ideal system for cold storage or freezing due to its high compaction and the resistance of roller and shuttle systems at low temperatures.
- Minimum operating costs due to excellent space optimisation.
Main applications of Push-Back Racking LIFO
Push-Back storage systems significantly optimise the available space in the warehouse, but due to their LIFO-type stock management, they do not enable such fast product turnover as Live Pallet Racking FIFO. They are therefore recommended for application in the following cases:
- Storage of homogeneous non-perishable products or products with a long expiration date.
- Warehouses with a wide variety of product references; each lane can be reserved for a specific type of reference.
- Warehouses with a low number of unit loads for each reference, since each lane can store a maximum of 6 unit loads, depending on the system used.
- Warehouses which, due to their storage needs, require the combination of the push-back system with other types of pallet racking or for manual picking.
- Possibility of installation in warehouses with cold rooms or freezing chambers.
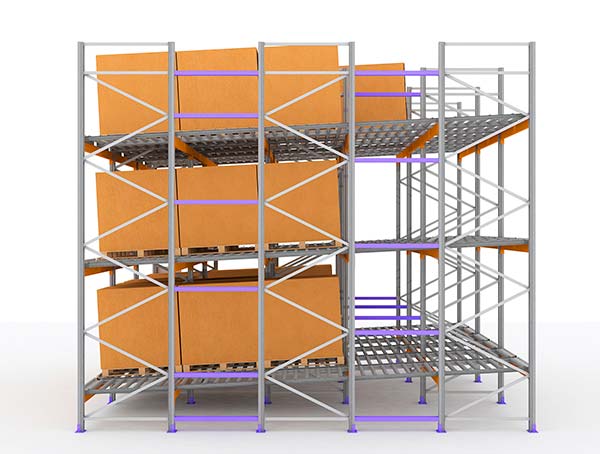
Push-Back Live Storage System Structure:
The Push-Back Live Storage Racking system for pallets consists of a base metal structure of frames, beams, crossbeams and dynamic profiles with the common quality features of the rest of AR Racking’s pallet racking systems.
The components that distinguish this system from the rest are its sets of shuttles or rollers which generate the live system and the movement inside the structure. These elements also include safety accessories for braking and controlling the unit loads.
Main components that make up Push-Back Racking LIFO are:
Galvanised frame
The galvanised frame, as in other storage systems, is one of the basic racking components and consists of 2 galvanised uprights, their diagonals, baseplates and floor fixing elements.
Beam
Beams are the horizontal components that indirectly support the load and that join the frames together. In push-back racking LIFO, the beams support the roller beds or the shuttles that enable the movement of the pallets inside the structure.
The beams are joined to the galvanised uprights being inserted into the drill holes of the upright by means of the connectors.
Push-Back Racking LIFO protectors
They are passive safety elements which protect the racking from potential forklift impacts.
Profile
Component anchored to the beams of each of the level ends and on which the shuttles or rollers that move the racking are supported.
Pallet guidance
It is situated at the front of each level, on each side of the lane, to help operators when depositing the unit loads and to prevent them from veering from their correct course. It also acts as a protection against potential impacts to the shuttle or roller system.
Pallet backstops
Component located at the start of the lane, in the loading and unloading area which in push-back racking is the same. Their objective is to stop the pallet which is in first position ready for its removal.
Push-Back roller system
It is one of the two variants for the operation of this system and is the basic component in Push-Back Racking LIFO, designed in steel and with the rails along the entire level with an upward incline to facilitate compaction thanks to the pushing force.
Push-Back shuttle system
This is the other possible alternative for this system, consisting of shuttles and rails to enable the movement of the shuttles.
The rails are steel elements fixed to the beams with a slight incline to facilitate the movement of the pallets.
The shuttles are connected to them, adaptable in size and number depending on the characteristics of the unit load and the depth of the lane.
The design of Push-Back pallet racking LIFO systems complies with the strictest international safety standards, and also includes AR Racking’s guarantee of excellence.
5-year quality guarantee
The quality reliability of our pallet racking solutions means we are able to offer 5-year quality guarantees against all types of manufacturing or hidden defects in the components of the main structure of our racking solutions.
100% automated production
Our push-back racking basic component production process is fully automated in our production centre: it incorporates state-of-the-art profiling machines with a continuous cutting process and laser measurement control, welding centres and automated painting and packaging processes, which guarantee the highest quality parameters.
Pioneering traceability system
Our pallet racking uprights and beams include a pioneering traceability system in the sector. With this system, our storage system components have an identifying mark, which means that each upright and beam can be traced and documented, and that information is therefore available on its design and the raw material used in its manufacture.
Designs in R&D&I Centre
Our Push-back Pallet racking systems are designed and calculated in our exclusive technology centre where we have an expert technical team which allows us to tackle projects with diverse logistics requirements.
Tests at Research and Testing Laboratory
The Research and Testing Laboratory developed in collaboration with the University of Mondragón provides our product area with the appropriate tools for the testing and analysis of our push-back pallet racking systems.
It simulates, calculates and researches the efficacy of the geometries, and makes full structural calculations on the behaviour of systems already installed.
LIFO Push-Back Racking for pallets meets the following standards:
- ISO 9001: 2008
- ISO 18001: 2004
- OSHAS 18001: 2007
- Welding certificate: UNE EN ISO 3834-2: 2006
- Galvanized steel corrosion resistance certificate: UNE EN ISO 14713-1
- Galvanized steel reaction to fire: EN 13501-1: 2007
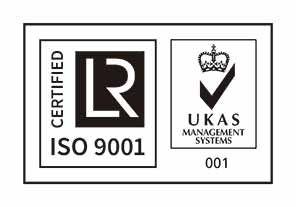
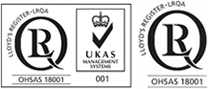
References
The best example of our good work optimising our customers’ warehouses is their satisfaction in the more than 26,000 projects carried out in over 60 countries.
We are proud to have customers from various sectors: food and beverage, automotive, distribution, electronics, pharmacy and cosmetics, industrial and transport and logistics.
Some featured projects of Push-Back Racking (LIFO):
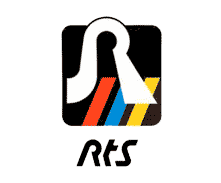
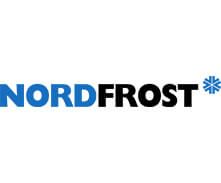